Blog Near-Net Shaping Process: Featured Solution Examples
By: Dave Olsen
Think of a problem that you face in metal component design or application. Here are some near-net shape manufacturing examples of where leveraging the advantages of near-net shaping have helped MetalTek and a customer work together to solve an application challenge. Maybe you will see a problem you are working to resolve. For more information regarding any of your metal applications, please Contact Us.
Near-Net Shaped Centrifugals Reduce Scrap Costs
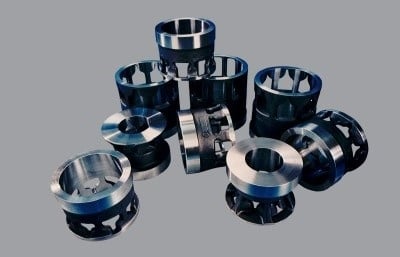
When supplied as a static casting, defects in certain valve components are often not discovered until much machining had been completed. The results are very high scrap rates and cost. Working with a specific customer-facing this, MetalTek engineers converted the static casting to a centrifugal, incorporating sand core technology into the design of the existing part. The homogeneous quality of a centrifugal casting reduced hidden defects. The rough casting was designed so that the last machining pass on the I.D. of the part opened the windows, minimizing the number of interrupted machining cuts. This further drove down scrap, which has been reduced by 98%.
Net Shaping Reduces Machining Costs

Compressor cases for critical jet engine applications typically consist of forgings which require extensive machining of excess material to yield a finished part. In a typical application, as much as 90% of the original material will be machined away. To reduce the need for such extensive pre-processing, MetalTek developed net-shaped centrifugals, a hybrid of investment and centrifugal processes. By casting in much of the shaping that would otherwise need to be machined in, this technology can save as much as 80% of the needed machining per part. In addition, the cost to unnecessarily add pounds of expensive exotic alloy materials in the cast part can be avoided, without compromising the quality of the final component.
Near-net Shaping Replaces Costly Fabrication
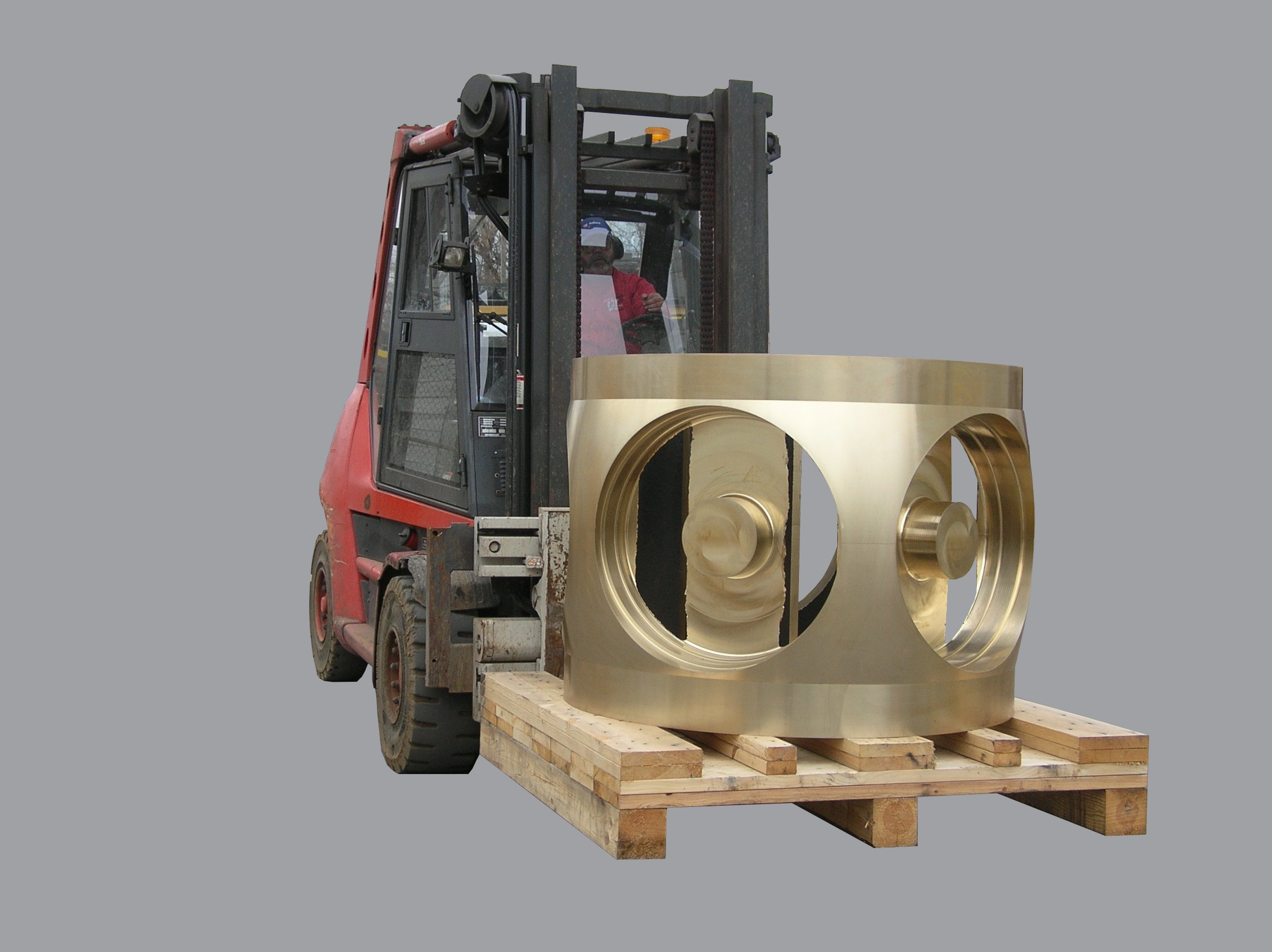
Large propulsion components used in naval applications are subject to high stresses for prolonged periods and must deliver high-strength performance in corrosive environments for the life of the vessel. Fabrications previously used in this application were very intricate, with multiple pieces and welds, and much machining. The single-piece MetalTek centrifugally cast nickel aluminum bronze hub eliminates welded joints and fabrication defects that are only discovered after finish machining.
Near-net Shaping Reduces Machining and Cost While Offering Superior Quality
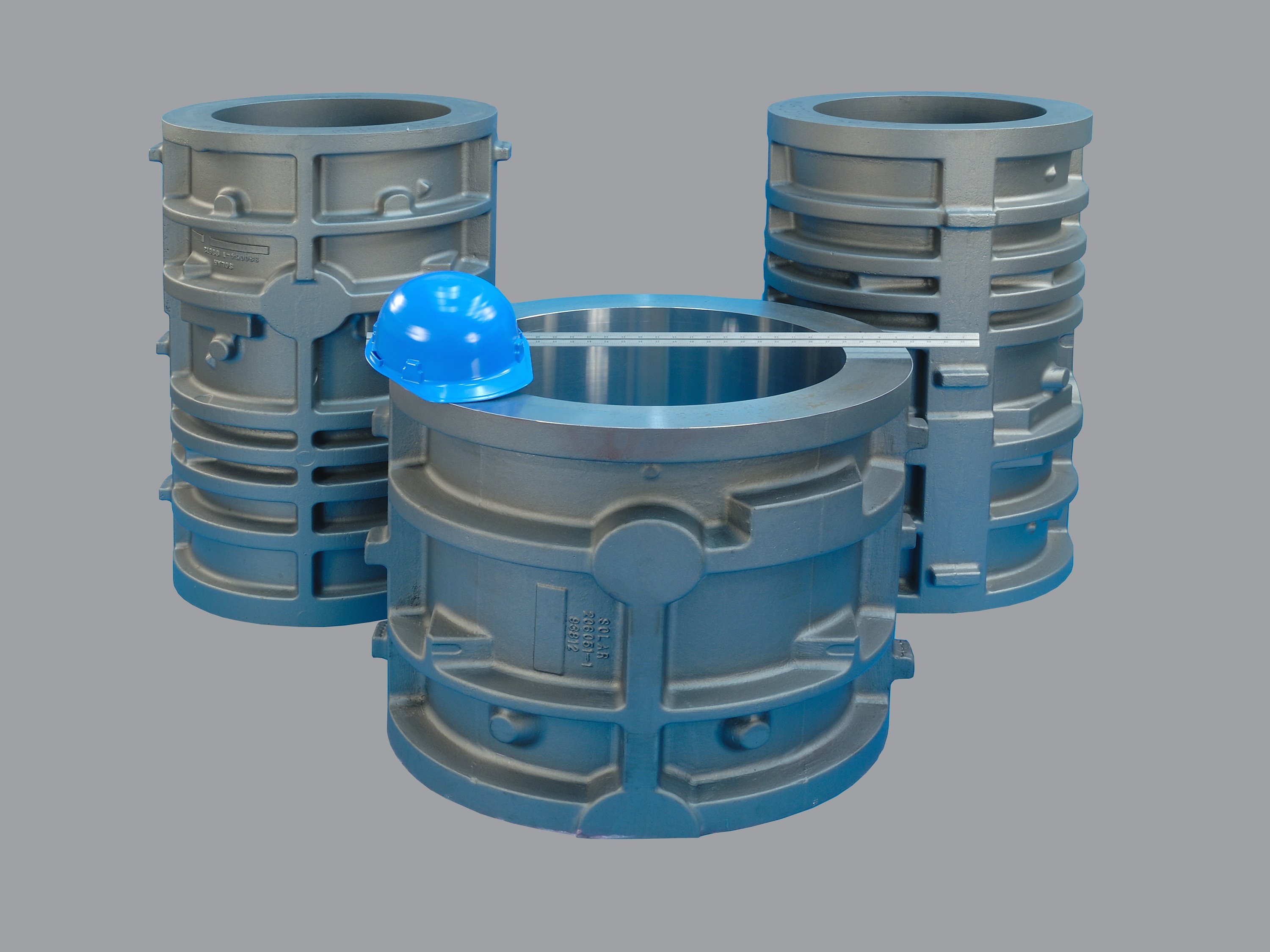
Shaping and internal metal soundness have always been a challenge for medium to large structural castings. MetalTek International provides a solution to this need by combining near-net shaping capabilities with the superior centrifugal process. Because large features are cast in, machining and processing costs are significantly reduced when compared to fabrications and hog-outs. Producing these O.D. features with the centrifugal process provides superior metallurgical and structural integrity throughout the part wall, a perfect fit for high temperature and pressure applications. With the ability to produce net-shaped parts in sizes of 50” (1270mm) tall and 80” (2032mm) in diameter or more, this innovative hybrid casting method reduces material cost and machine time eliminating the need for expensive milling operations.
The versatility of near-net-shape casting helps turn metals problems like these into successes. To learn more about the near-net-shape casting process or determine if it is a fit for your application, please Contact Us.