Blog Shaped Centrifugal Castings
By: Dave Olsen
Centrifugally cast components are typically thought of as straight walled cylindrical geometries such as tubes, pipe, or rings. They are often cast horizontally in permanent steel dies that have a removable end cap. Because the part must be extracted from the uncollapsible die, shaping is limited to geometries that have a straight or slightly drafted O.D.
While the majority of centrifugals are straight-walled pipe or tubing cast horizontally, it is common for centrifugals to have more complex shapes.
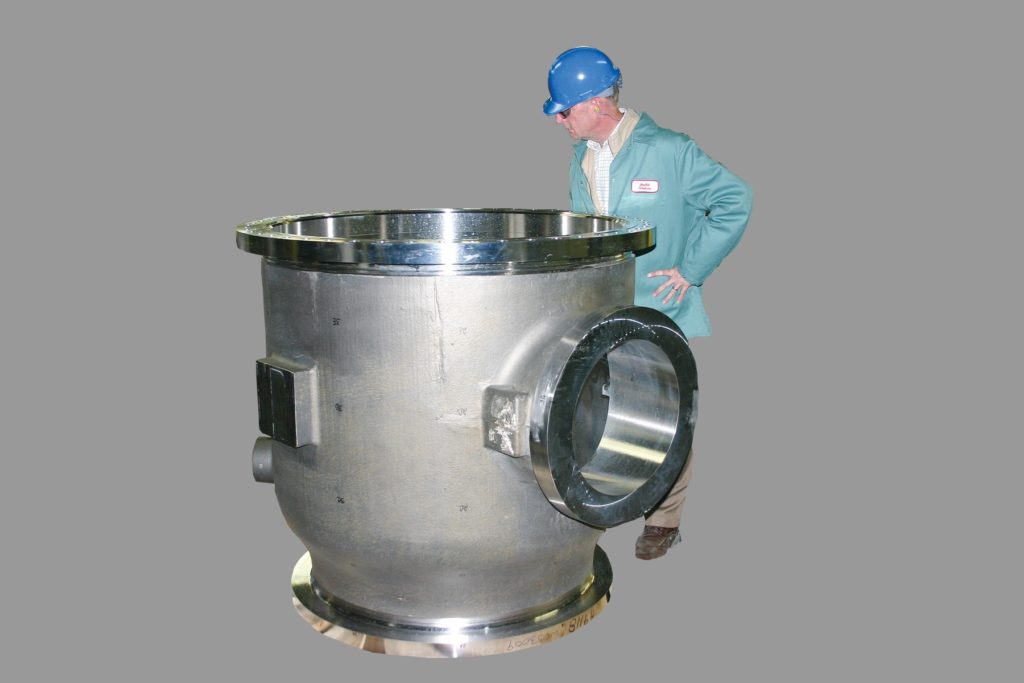
MetalTek utilizes a vertical axis of rotation and more complex dies using tapers, counterturns, and removable sections to produce centrifugals with cast flanges, tapered walls, and asymmetric geometries. Near-net and net-shaped centrifugals are typically poured into a vertically spinning, formed, consumable mold. The mold is typically sand, ceramic, graphite, metal, or a combination, depending on geometric complexity, size, production process, etc. The result is a part that may require virtually no O.D. machining.
While the process is most amenable to outside shaping, advances in process and molding materials can result in some limited I.D. shaping as well. The fluid and solidification dynamics typical of straight walled, permanent die centrifugals, apply to shaped centrifugals as well. This results in directional solidification from O.D. to I.D. and molten metal refinement due to the centrifuging of low density impurities to the bore. As in straight walled centrifugal castings, shaped centrifugals are machined in the bore to remove the impurities.
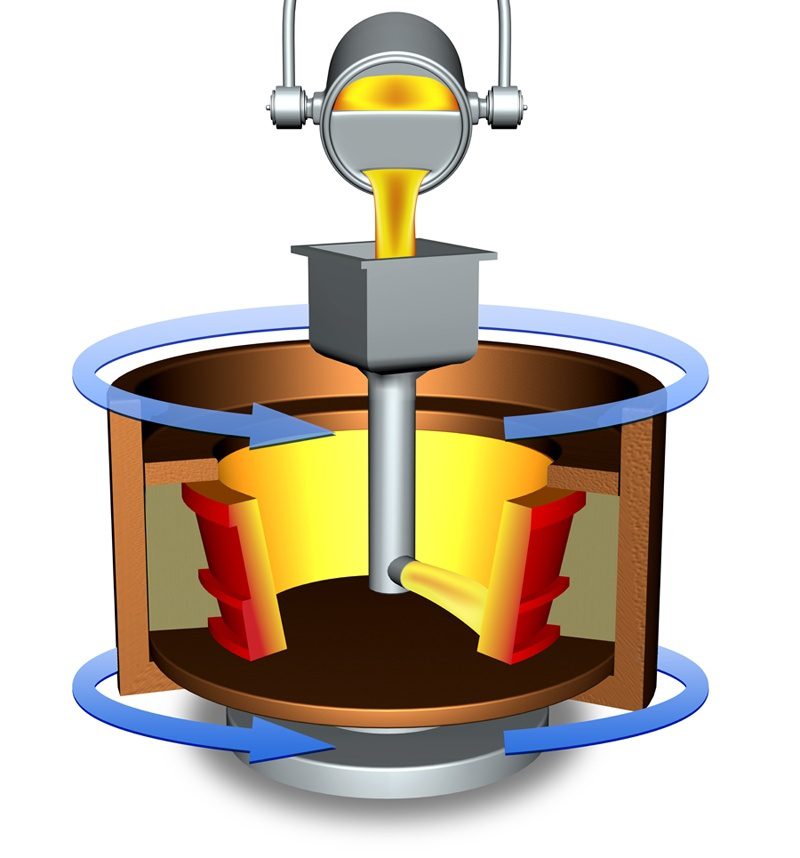
Components produced as shaped centrifugals also do not necessarily have to be symmetric about the axis of rotation. Geometries with flanges on each end face, or flanges and other features protruding from the side wall can be produced. Parts that are well suited for the shaped centrifugal process include parts with mostly external features, that require at a high level of product integrity.
The finished cost of a component cast as a shaped centrifugal may be considerably lower than for a straight-walled component because greatly reduced machining costs can more than offset the slightly higher mold and processing costs of a shaped centrifugal. For example, one MetalTek customer converted a straight-walled forging to a net shaped centrifugal and eliminated eight weeks of machining on a five-axis mill, significantly reducing the component cost, while maintaining product quality.
Other customers convert from forgings and fabrications to shaped centrifugals to eliminate the fabrication welding required for flanges and volutes. Those features can be cast integrally into a shaped centrifugal.
For many applications, a shaped centrifugal offers exactly the right solution.